Wet Ball Mill Iron Ore Grinding
.jpg)
A Review of the Grinding Media in Ball Mills for Mineral
2023年10月27日 Grinding media play an important role in the comminution of mineral ores in these mills This work reviews the application of balls in mineral processing as a function of the materials used to manufacture them and the mass loss, as influenced by three basic wear The paper demonstrates the application of this methodology to optimize solids concentratioOptimization of Solids Concentration in Iron Ore Ball Millin2019年9月1日 Dry grinding consumes higher energy and produces wider particle size distributions compared with wet grinding It significantly decreases the rate of media A comparative study on the effects of dry and wet grinding 2024年9月24日 High Pressure Grinding Roll (“HPGR”) technology is applied to an increasingly diverse range of applications, predominantly iron, gold and diamonds KHD Humboldt Wedag HIGH PRESSURE GRINDING MOVING AHEAD IN
.jpg)
Impact of ball filling rate and stirrer tip speed on milling iron ore
2021年1月22日 The wet grinding of iron ore powder was investigated using a stirred media mill In this study, the fitting degree of four cumulative undersize distribution functions was 2023年11月28日 In response to the Natural Resources Canada “Crush It Challenge,” Corem partnered with the University of British Columbia and led a project to develop and demonstrate Replacement of Wet Ball Milling with HighPressure Grinding 2020年5月15日 Modern iron ore pelletizing process operations may be divided into two main process sections: feedstock preparation and agglomeration processes In most plants, the Development of a Novel Grinding Process to Iron Ore2007年10月19日 Comparison of simulated (without exit classification) and experimental size distributions from wet grinding of iron ore in the pilotscale millSimulation of wet ball milling of iron ore at Carajas, Brazil
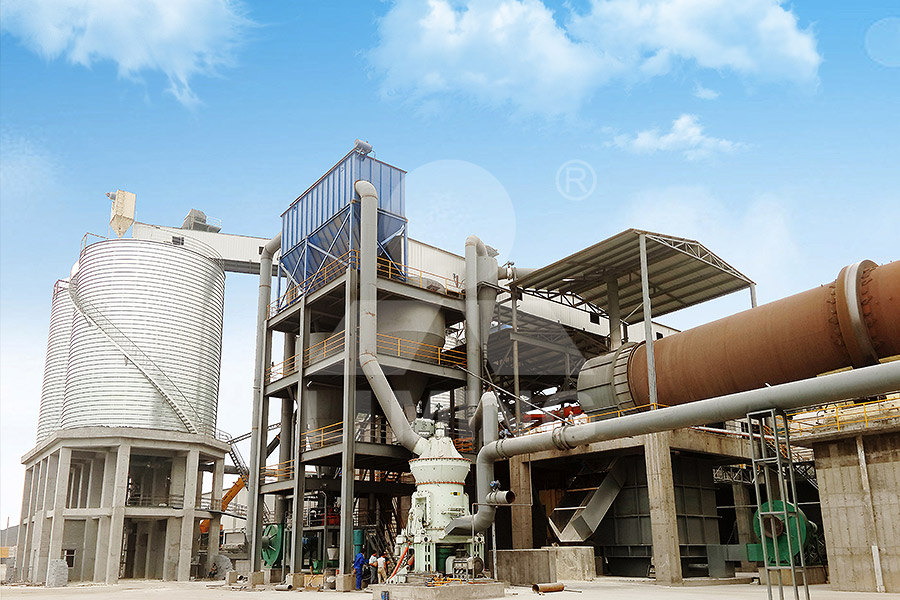
Simulation of wet ball milling of iron ore at
2007年10月1日 Laboratoryscale batch grinding tests were performed on 2 sieve size fractions of the almost pure hematite mined at the Carajas mine of CVRD Brasil Good firstorder kinetics of grinding wereIn this chapter the mechanisms of wetgrinding mills are considered The nature of the forces at work, together with a detailed consideration of their interplay and means of control, are WetGrinding Mills SpringerLink2007年10月1日 A Firstorder plots for batch dry grinding of feeds of 16 × 20, 35 × 45, 45 × 60 mesh iron ore B Firstorder plot for dry grinding of 4 × 6 mesh (oversized particles) iron ore: effective S Simulation of wet ball milling of iron ore at 2024年1月2日 1 Population balance model approach to ball mill optimization in iron ore grinding Patricia M C Faria1,2, Luís Marcelo Tavares2 and Raj K Rajamani3 1 Vale SA, Brazil 2 Department of Population balance model approach to ball mill
.jpg)
Buy Ore Ball Mill for Mineral Processing Iron
Ore ball mill sometimes called ore grinding mill, is generally used in mineral processing concentrator, processing materials include iron ore, copper ore, gold ore, molybdenum ore and all kinds of nonferrous metal oreThe core function DOI: 101016/JPOWTEC202107030 Corpus ID: ; Mechanistic modeling and simulation of grinding iron ore pellet feed in pilot and industrialscale ball mills @article{Carvalho2021MechanisticMA, title={Mechanistic modeling and simulation of grinding iron ore pellet feed in pilot and industrialscale ball mills}, author={Rodrigo M de Carvalho and Mechanistic modeling and simulation of grinding iron ore The general term “tumbling mill” includes the rod mill, pebble mill, and ball mill It is of cylindrical or cylindroconical shape, and rotates about a horizontal axis A load of crushing bodies called the grinding media forms part of the crop load They bear upon the piece of ore in the tumbling mixture with abrasive and/or impacting force WetGrinding Mills SpringerLink2023年10月27日 The ball mill is a rotating cylindrical vessel with grinding media inside, which is responsible for breaking the ore particles Grinding media play an important role in the comminution of mineral ores in these mills This work reviews the application of balls in mineral processing as a function of the materials used to manufacture them and the mass loss, as A Review of the Grinding Media in Ball Mills for Mineral
.jpg)
(PDF) Grinding Media in Ball MillsA Review ResearchGate
2023年4月23日 balls grind coarser ore particles efficiently and smaller balls grind fine particles more efficiently [44] Larger balls break particles by impact, whilst smaller balls break by abrasion2020年11月13日 1) Structure The shape and components of the wet ball mill and the dry ball mill are basically the same The barrel is cylindrical, and the structure mainly includes the feeding part, the discharging part, the rotating part, the transmission part (reducer, small transmission gear, motor, electric control), etcDry Ball Mill VS Wet Ball Mill: What Are the Differences2020年10月18日 An iron ore concentrate sample was ground separately in a pilotscale HPGR mill in multiple passes and a dry opencircuit ball mill to increase the specific surface area of particlesThe effects of iron ore concentrate grinding methods (HPGR and Ball 2019年6月18日 demonstrates the application of this methodology to optimize solids concentration in ball milling of an iron ore from Brazil The wet grinding experiments were conducted in bench (025 m diameter) and pilotscale mills (042 m diameter), and surveys in a fullscale industrial (52 m diameter) mill It is firstOptimization of Solids Concentration in Iron Ore Ball
.jpg)
Morphology and wear of high chromium and austempered ductile iron balls
2021年11月1日 The grinding wear conduct of both materials is evaluated for wear loss in wet grinding conditions of austempered ductile iron as grinding media material for grinding the iron ore in a ball 2024年1月13日 Table 1 Chemical composition of typical grinding media (% wt) Adapted from [24] 211 Cast Iron Cast iron can be grey cast iron or white cast iron, but white cast irons are commonly used in Grinding Media in Ball MillsA Review ResearchGate2023年11月28日 In response to the Natural Resources Canada “Crush It Challenge,” Corem partnered with the University of British Columbia and led a project to develop and demonstrate the use of highpressure grinding to replace the workhorse of the industry, wet ball milling Two plant case studies, a small tonnage gold recovery operation and a large tonnage copper recovery Replacement of Wet Ball Milling with HighPressure Grinding Mobile Stone Iron Gold Ore Rock Mining 100150 Tph Jaw Crusher Manufacturers Price Portable Granite Crushing Machine Plant for Sale US$8,9600029,64600 / Set 1 Set (MOQ) China Good Quality Energy Saving 35tph Wet Gold Ball Mill Machine for Grinding Quartz Limestone Gold Ore Factory Price US$6,0000036,50000 / Set 1 Set (MOQ)Jaw Crusher Manufacturer, Hammer Cruser, Cone Crusher
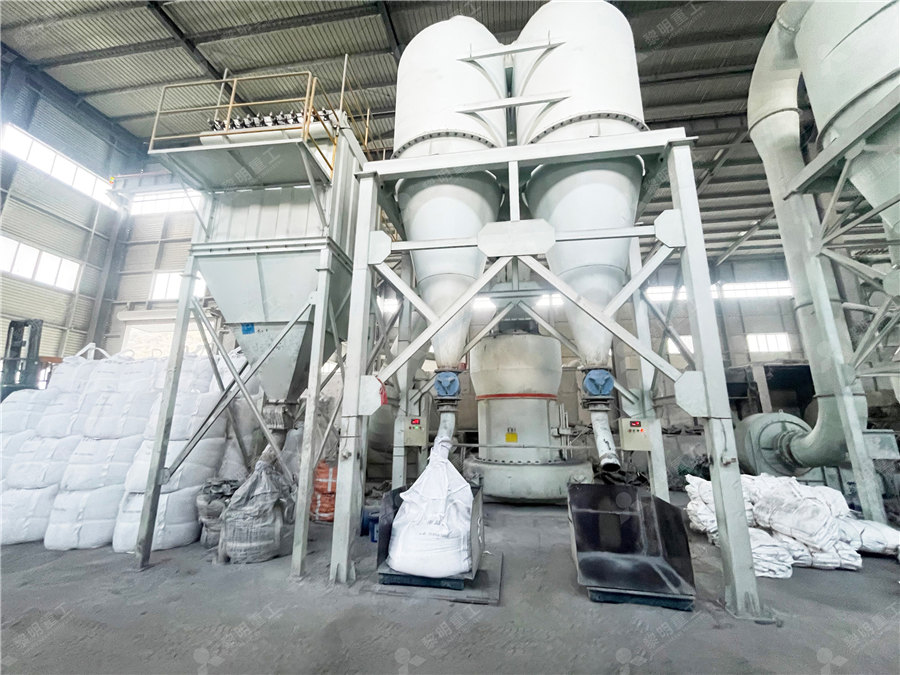
Dry Grinding Vs Wet Ball Mill Grinding Economy Ball Mill
2023年9月15日 To get a better idea of dry ball mill grinding and wet ball mill grinding, let’s first look at the differences between the two associated machines Dry grinding machine : A dry grinding machine uses no liquid element and relies on particleonparticle contact to reduce the size of the materials2019年9月1日 To select dry or wet grinding, the differences between their process conditions should be taken into consideration Transfer and motion of particles by air in case of dry grinding or water may significantly affect power draw and energy consumption of grinding circuits [5]Particularly, these energy differences become significant when considering that around 3% A comparative study on the effects of dry and wet grinding The results of the analyses clearly shows that using a sieve of +180µm and its bottom 180µm, the best time for grinding 05kg of Itakpe iron ore with 3kg of grinding media and a mill speed of 92 rpm is 8 minutes, yielding 1710% fines and 8290% coarse, 08 mill critical speed measured 1520% fines and 8480% coarseSimulation of wet ball milling of iron ore at Carajas, Brazil2023年2月15日 Most of the ball mill types sold on the market are wet ball mills, as they have high grinding fineness and good beneficiation effect As dry and wet ball mills both have their own advantages, we must find out the suitable grinding type to ensure the production quality and efficiency Welcome to consult Fote company, where our professionals will What Are the Differences between Dry and Wet Type Ball Mill?
.jpg)
Friction and wear of liner and grinding ball in iron ore ball mill
DOI: 101016/JTRIBOINT201706017 Corpus ID: ; Friction and wear of liner and grinding ball in iron ore ball mill @article{Peng2017FrictionAW, title={Friction and wear of liner and grinding ball in iron ore ball mill}, author={Yuxing Peng and Xu Ni and Zhencai Zhu and Zhangfa Yu and Zixin Yin and Tongqing Li and Liu Songyong and Lala Zhao and Jie Xu}, 2020年3月28日 The main binding force in wet iron ore green pellets has been found to be the cohesive force of the viscous binder as well as by comminution tests in a benchscale ball mill and highpressure Development of a Novel Grinding Process to Iron Ore Advantages of Ball Mill Ball mill grinding machine offer several advantages, including: Versatility: Ball mills can perform various types of grinding, such as dry grinding ball mill or wet grid ball mill, batch or continuous grinding, and fine or ultrafine grinding, making them Ball Mill Grinding Machines: Working Principle, Types, Parts The results of the analyses clearly shows that using a sieve of +180µm and its bottom 180µm, the best time for grinding 05kg of Itakpe iron ore with 3kg of grinding media and a mill speed of 92 rpm is 8 minutes, yielding 1710% fines Simulation of wet ball milling of iron ore at
.jpg)
wet beneficiation of iron ore Grinding Mill China
The most commonly used crushers and grinding mills in iron ore crushing and grinding process for iron ore mining are Jaw Crusher, Cone Crusher, Hammer Crusher and Ball Mill, SCM Micro Mill, etc In iron ore mining, miner usually choose a complete iron ore crushing plant for metallurgy Iron ore beneficiation process Almost all of the iron ore 2013年8月1日 Albertin and Sinatora (2001) have considered the effect of carbide volume fractions from 13% to 41% and matrix microstructure on the wear of 50 mm diameter cast iron balls tested in a laboratory ball mill during wet grinding of hematite, phosphate rock and quartz sand Martensitic, pearlitic and austenitic matrices were evaluatedConsumption of steel grinding media in mills – A review2023年5月9日 POPULATION BALANCE MODEL APPROACH TO BALL MILL OPTIMIZATION IN IRON ORE GRINDING* Patrícia Mundim Campos Faria1 Luís Marcelo Tavares 2 Raj K Rajamani 3 model in wet grinding system was established through detailed experimentation carried out in a 0254 m batch mill diameter In order to validate the methodologyPOPULATION BALANCE MODEL APPROACH TO BALL Wet ball mill is a kind of equipment which uses grinding medium and a certain amount of liquid (water or anhydrous ethanol) to grind materials Unlike dry ball mill, wet ball mill adopts the wet grinding method The characteristic of wet grinding is that the material needs to be soaked in the liquid for grinding This method can effectively reduce the chance of the material properties Wet Ball Mill for Metal Ores and Nonferrous Metals Wet
.jpg)
Effect of chemical additives on the dynamics of grinding media in wet
1985年11月1日 Recent papers on the role of grinding aids in wet ball mills indicate that certain poly meric aids favorably act by altering pulp rheology, leading to improved production rates at high pulp densities Analysis of recent data indicates that there can be an improvement in terms of the production of fine particles per unit time, but on the other 2017年11月1日 To understand the friction and wear of working mediums in iron ore ball mills, experiments were conducted using the ball cratering method under dry and wet milling conditions, which mimic the operating conditions in ball mills The liner sample is made of Mn16 steel, the ball had a diameter of 25 mm and was made of GCr15 steel, and the iron ore powder was Friction and wear of liner and grinding ball in iron ore ball mill 2007年10月19日 At Carajas, the new grinding plant was operational in 2002, with two ball mill lines followed by a desliming plant The closed circuit, wet grinding mills were designed to operate at 600% circulating load, in order to minimize the production of fine particles and consequently give increased recovery at the desliming plantSimulation of wet ball milling of iron ore at Carajas, Brazil2021年1月22日 Semantic Scholar extracted view of "Impact of ball filling rate and stirrer tip speed on milling iron ore by wet stirred mill: Analysis and prediction of the particle size distribution" by Wang Guo et al A potential ceramic ball grinding medium for optimizing flotation separation of chalcopyrite and pyrite Xiaolong Zhang Yonghong Qin +4 Impact of ball filling rate and stirrer tip speed on milling iron ore
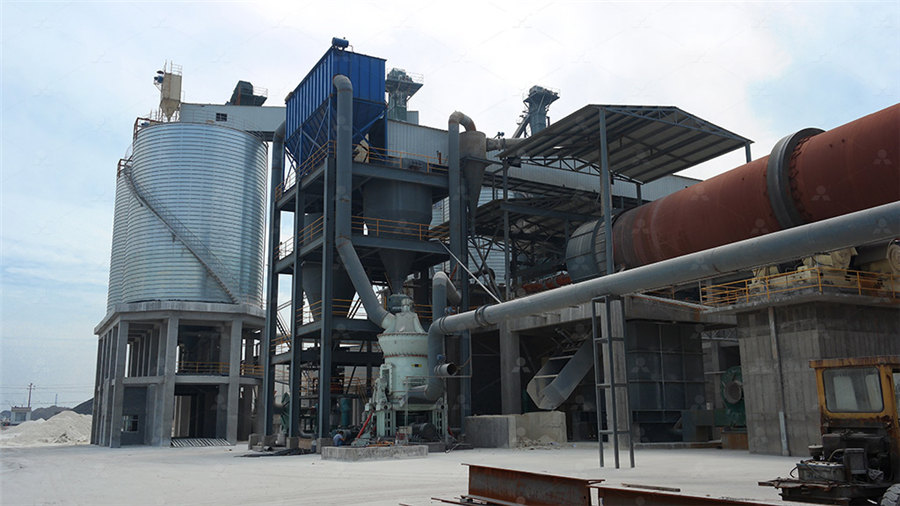
Optimization of Solids Concentration in Iron Ore
2019年6月18日 The wet grinding experiments were conducted in bench (025 m diameter) and pilotscale mills (042 m diameter), and surveys in a fullscale industrial (52 m diameter) mill2023年7月20日 Therefore, the rod mill is mostly used for coarse grinding of the previous period of ball mill, or grinding of brittle materials and materials against overcrushing, such as tungsten and tin ore before gravity separation; and (3) autogenous mill – it refers to the materials which themselves are collided and ground mutually to be crushed when Ore Grinding SpringerLink2024年2月26日 Oxidised pellets have become an indispensable highquality charge for blast furnaces Nevertheless, highquality pellet feeds are becoming scarcer and scarcer To broaden the range of sources of pellet feeds and Grinding of Australian and Brazilian Iron Ore 2022年3月19日 The Iranian GoharZamin iron ore beneficiation plant consists of equipment such as gyratory and cone crushers, high pressure grinding rolls (HPGR), ball mill, dry and wet doubledeck vibrating Grinding iron ore concentrate by using HPGR and ball mills
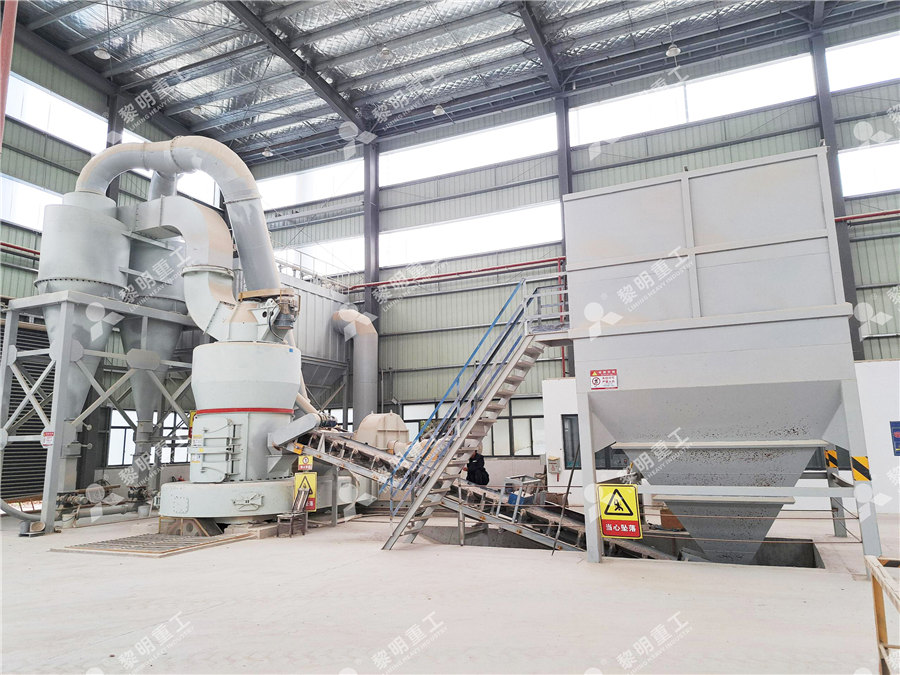
Impact of ball filling rate and stirrer tip speed on milling iron ore
2021年1月22日 The wet grinding of iron ore powder was investigated using a stirred media mill In this study, the fitting degree of four cumulative undersize distribution functions was compared and the parameters of the four functions were discussed Xiao et al [2] investigated the iron grade and recovery of fine grained magnetite ground by a stirred 6 天之前 Wet Pan MillWet Pan Mill, also called Wet Pan Mill, is mainly working for preliminary grinding for gold, silver, lead, zinc, iron, and copper ore concentration, but also one of the main milling machines to replace of ball mill Our pan mill is suitable for smallscale wet pan mill Jiangxi Hengcheng Mining Equipment Co, Ltd2015年6月19日 Ball Mill Power/Design Calculation Example #2 In Example No1 it was determined that a 1400 HP wet grinding ball mill was required to grind 100 TPH of material with a Bond Work Index of 15 (guess what mineral type it is) from 80% passing ¼ inch to 80% passing 100 mesh in closed circuit What is the size of an overflow discharge ball mill for Ball Mill Design/Power Calculation 911Metallurgist2013年8月3日 In Grinding, selecting (calculate) the correct or optimum ball size that allows for the best and optimum/ideal or target grind size to be achieved by your ball mill is an important thing for a Mineral Processing Engineer AKA Metallurgist to do Often, the ball used in ball mills is oversize “just in case” Well, this safety factor can cost you much in recovery and/or mill liner Calculate and Select Ball Mill Ball Size for Optimum Grinding
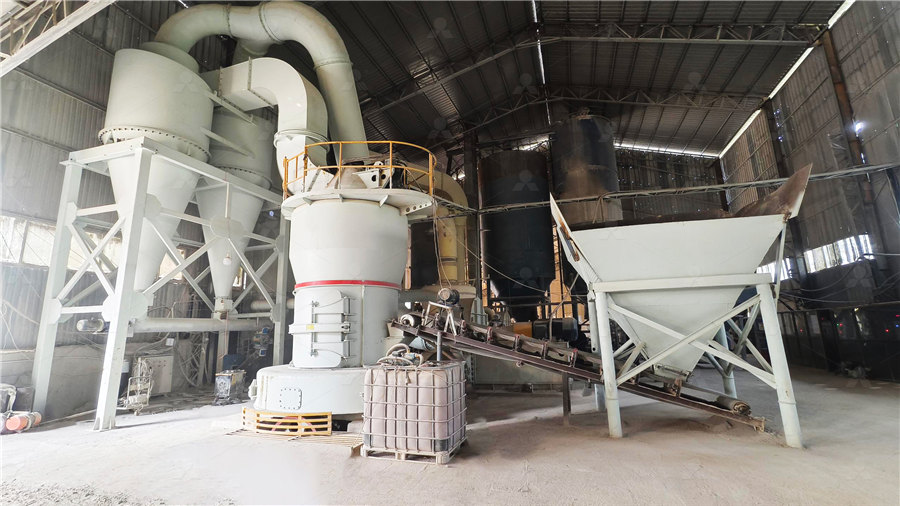
Ball Mill Rotary Kiln Vertical Roller Mill Manufacturer Tongli
Iron ore vertical roller mill Silica sand vertical roller mill Wet ball mill Grid Ball Mill Rod mill Conical Ball Mill And Design Ore Ball Mill Center drive ball mill Edge drive ball mill A cement ball mill is a tube grinding machine that used to grind materials into 2016年1月1日 The effect of using conventional and high pressure grinding rolls (HPGR) crushing on the ball mill grinding of an iron ore was assessed to determine how these different comminution processes A comparative study on the effect of using conventional and